Sustainability
Reverse Logistics
What is Reverse Logistics? A Comprehensive Introduction
By G2RL Team
Mar 3, 2025
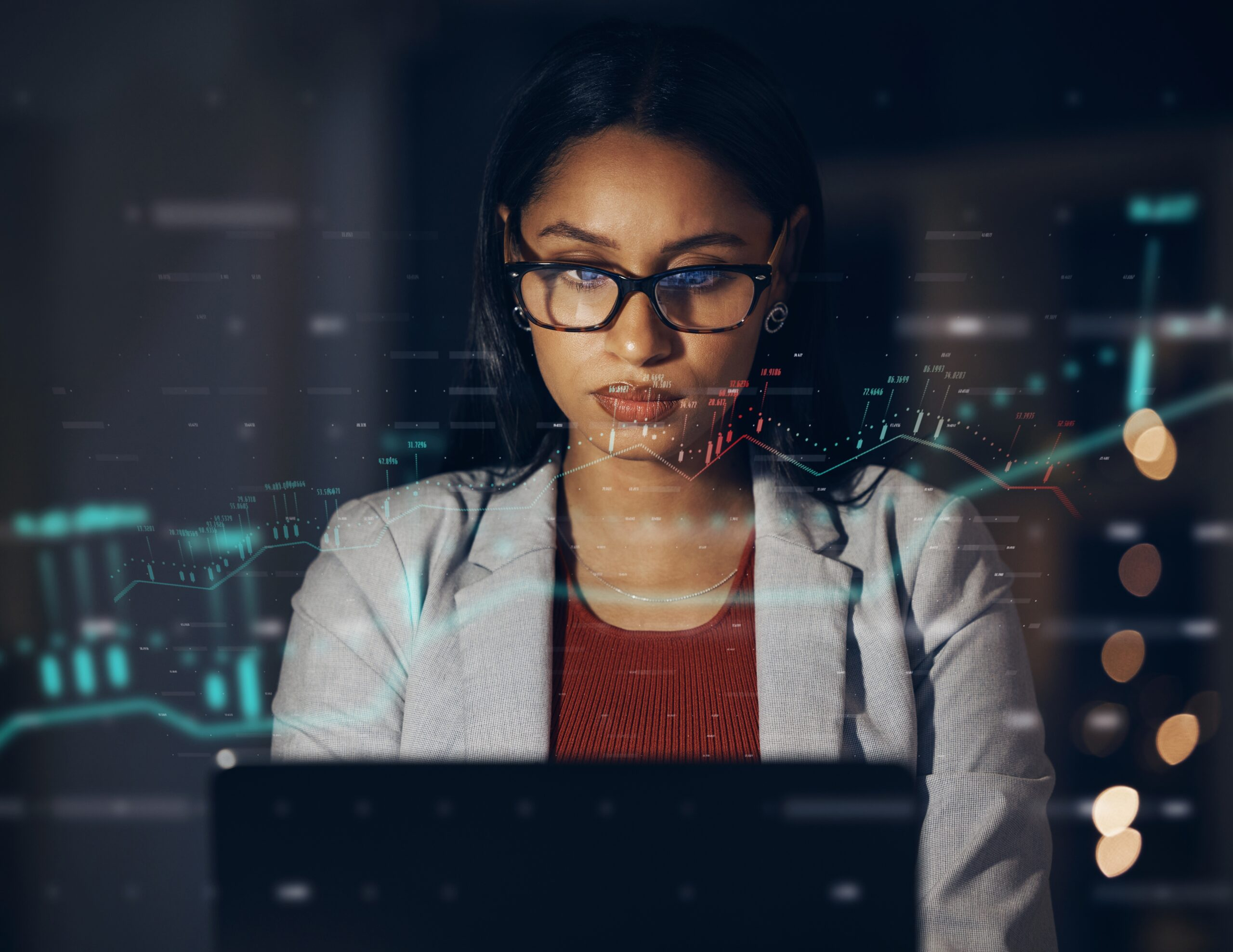
Table of Contents
Key Reverse Logistics Processes
1. Cost Savings & Revenue Recovery
2. Enhanced Customer Satisfaction & Brand Loyalty
3. Sustainability & Compliance
4. Operational Efficiency & Data-Driven Insights
Common Reverse Logistics Challenges
4. Compliance & Regulatory Risks
How to Optimize Reverse Logistics
1. Leverage Technology & Automation
2. Improve Visibility & Data Analytics
3. Enhance Customer Experience
4. Strengthen Partnerships with IT Asset Disposition (ITAD) Providers
5. Sustainability-Focused Reverse Logistics
Why Should You Outsource Your Reverse Logistics?
1. Ability to Focus Better on Core Functions
If you are a retail or an eCommerce business, reverse logistics might be one of the business terms that you dread the most. After all, reverse logistics seems like a nightmare that costs your company additional money, cuts into your profit, and results in a loss of value.
But now, reverse logistics has become a fact of life for most businesses, all thanks to the explosion of eCommerce. Today, if a company wants to achieve high levels of customer satisfaction and repeat business, it needs to have a hassle-free reverse logistics process. Don’t believe it? According to one study, 92% of consumers will buy something again if returns are easy. Moreover, the returns process influences purchasing decisions to such a great extent that 67% of shoppers check the returns page before buying a product.
So now it has become more important than ever for businesses to effectively manage their reverse logistics process. In this guide, we’ll explore what reverse logistics is, its benefits, challenges, and how businesses can leverage technology to turn returns into a strategic advantage.
What is Reverse Logistics?
Reverse logistics is the process of returning products from the customer to the seller, distributor, or manufacturer. It is essentially a reverse supply chain. Returns occur for various reasons like customers returning unwanted products, sellers sending unsold inventory back to wholesalers or suppliers, and manufacturers receiving faulty or used goods for repair, refurbishment, or recycling.
The goal of reverse logistics is to ensure proper product disposition, enhance customer satisfaction, and maximize net recovery by optimizing the value of each return. Depending on the product’s condition, returns may be resold, reused, repurposed, or disposed of through the most efficient and sustainable channel.
While businesses traditionally prioritize sales growth, they also need to manage the complex logistics of returns and refunds. Well-structured reverse logistics operations help businesses determine the best destination for returned items whether a warehouse, factory, recycling plant, or secondary marketplace while minimizing costs and inefficiencies. Without a strategic approach, companies risk higher expenses, tracking difficulties, and productivity losses from manual processes.
Once seen as an operational burden, reverse logistics is now recognized as a key driver of profitability, brand credibility, and sustainability. Businesses can turn returns into revenue-generating opportunities while improving customer loyalty and environmental responsibility.
Key Reverse Logistics Processes
- Returns Management – Handling customer returns, ensuring seamless processing, restocking, or reselling.
- Refurbishment & Repair – Repairing or refurbishing returned products for resale or reuse.
- Recycling & Disposal – Ensuring eco-friendly recycling or disposal of products at the end of their lifecycle.
- Recommerce & Resale – Identifying recommerce opportunities for reselling returned goods through secondary markets.
- Asset Recovery – Extracting value from returned products through liquidation or parts harvesting.
Benefits of Reverse Logistics
1. Cost Savings & Revenue Recovery
Returns don’t have to be a financial drain. Businesses can reduce costs by:
- Refurbishing and reselling returned items instead of discarding them.
- Recovering valuable materials from used or damaged products.
- Reducing storage costs through optimized returns management.
2. Enhanced Customer Satisfaction & Brand Loyalty
Customers expect a seamless and hassle-free return experience. A well-managed reverse logistics process can:
- Encourage repeat business by offering flexible return policies.
- Reduce refund processing times, enhancing customer trust.
- Improve product quality by identifying and resolving recurring issues.
3. Sustainability & Compliance
Reverse logistics plays a crucial role in corporate sustainability initiatives:
- Recycling and repurposing returned goods reduce landfill waste.
- Proper disposal methods ensure compliance with environmental regulations.
- Circular economy practices allow businesses to reduce reliance on raw materials.
4. Operational Efficiency & Data-Driven Insights
Advanced reverse logistics systems can:
- Optimize returns routing to reduce handling and transportation costs.
- Provide real-time visibility into return trends, warranty claims, and product lifecycle insights.
- Predict return volumes and improve inventory management.
Common Reverse Logistics Challenges
1. Process Inefficiencies
Managing returns manually can lead to delays, higher costs, and errors in restocking, refurbishing, or disposing of products. Implementing automated dispositioning and AI-driven decision-making can streamline operations.
2. Financial Management
Returns handling costs, transportation, and labor expenses add up quickly. Budgeting for fluctuating return volumes is a challenge that requires advanced forecasting and cost-optimization strategies.
3. Third-Party Risks
Many businesses rely on third-party logistics (3PL) providers for returns management. Poor service quality or fraudulent practices by external partners can negatively impact customer experience and profitability.
4. Compliance & Regulatory Risks
Businesses must comply with data protection laws, environmental regulations, and product disposal guidelines to avoid fines and reputational damage.
How to Optimize Reverse Logistics
1. Leverage Technology & Automation
Reverse logistics software can automate the returns process, reducing manual effort and improving efficiency. Features like dynamic dispositioning and AI-driven fair market value (FMV) assessments ensure that returned products are routed to the most profitable recovery options.
2. Improve Visibility & Data Analytics
Capturing and analyzing return data helps businesses:
- Identify trends and recurring return reasons.
- Optimize inventory planning and reduce unnecessary returns.
- Enhance decision-making for repair, refurbishment, and resale strategies.
3. Enhance Customer Experience
A user-friendly product returns process can boost customer retention. Offering prepaid return labels, self-service return portals, and real-time return tracking are some ways businesses can improve the experience.
4. Strengthen Partnerships with IT Asset Disposition (ITAD) Providers
For tech hardware manufacturers, connecting with ITAD providers ensures that returned products are efficiently resold, torn down, or repurposed for component parts.
5. Sustainability-Focused Reverse Logistics
Implementing circular economy strategies ensures:
- Fewer products end up in landfills.
- More materials are reused or recycled.
- Businesses meet their sustainability targets while reducing operational costs.
Why Should You Outsource Your Reverse Logistics?
Although reverse logistics might not be your core business function, it has a major impact on customer experience. In instances where you do not have the resources, time, or expertise to handle your business’s reverse logistics, it is better to bring in the pros. Here’s why you should consider outsourcing your reverse logistics operations:
1. Ability to Focus Better on Core Functions
Managing reverse logistics calls for all of your business’s indispensable resources – time, labor, capital, space, and equipment. By outsourcing reverse logistics, you can focus more on the key business functions of product design and development, manufacturing, marketing, sales, and distribution.
2. Improved Inventory Management
Looking after your own reverse logistics entails tracking SKUs, monitoring product returns, considering storage space, arranging transportation, and ensuring real-time visibility of returns. Outsourcing eliminates these concerns, allowing businesses to focus on sales and customer service.
3. Exponential Growth
As your business grows, you’ll be overwhelmed by a growing number of orders. Efficiently handling returns without compromising customer experience and growth is critical. Outsourcing reverse logistics ensures scalability without added stress to your teams.
4. Benefit from Expertise
Reverse logistics providers have the resources and technology to offer a top-notch returns management experience. They also have agreements with carriers in place for transportation at reduced rates, leading to further cost savings for your business.
Learn About Choosing a Reverse Logistics Provider for Your Business
Conclusion
Reverse logistics is no longer just an operational necessity; rather, it is a strategic opportunity. By optimizing returns management, leveraging AI-driven reverse logistics systems like DecisionAI, and focusing on sustainability, businesses can reduce costs, recover lost revenue, and improve customer satisfaction.
Whether you’re a retailer, manufacturer, or distributor, investing in a robust reverse logistics strategy will position your business for long-term success.
Want to learn how G2RL can optimize your reverse logistics process? Contact us today for a demo and discover how AI-powered solutions can turn returns into revenue.
Reimagine reverse logistics.
Take the first step to smarter, more profitable returns. Talk to an expert today.